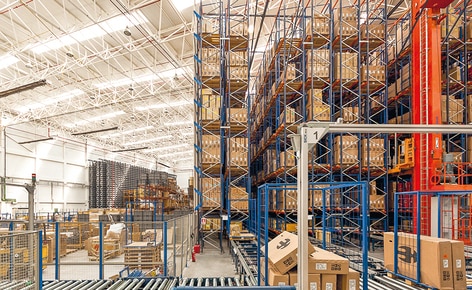
The bike manufacturer BH Bikes automates the storage of pallets and boxes in its new logistics centre in Vitoria
Stacker cranes for pallets, for boxes and P&D stations revolutionise logistics at BH Bikes
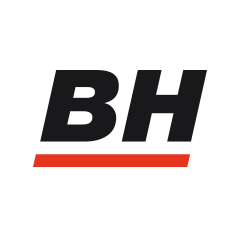
With the construction of this new centre, consisting of a miniload and an automated warehouse for pallets, the BH Bikes group has centralised all its logistics activities, improving customer service and reducing operating costs. In the provision, the Mecalux Easy WMS warehouse management software has also been included, which controls all the centre's activities.
BH Bikes: over 100 years of history
BH Bikes started in 1909 in Eibar (Basque Country) as a manufacturer of small arms. After World War II, it began to specialise in the manufacture of bicycles, a quick, economical and comfortable means of transport, which was popular at that time.
Over the years, the company became a benchmark in Spain thanks to the quality of its products and its constant innovation. Currently, BH Bikes is an internationally recognised company in the world of cycling.
Step one: analyse the needs of BH Bikes
The constant growth experienced by BH Bikes in recent years had forced them to store their products in several old buildings in the area. This emergency solution involved logistics costs and enormous management challenges.
The company saw that their facilities prevented them from growing and deploying advanced storage systems that help reduce operating expenses. In response, the management of BH Bikes decided to build a new storage and distribution centre, which could automatically store all their products.
Considering these premises, Mecalux's technical team worked from the outset with BH Bikes in the development and construction of a logistics centre that would cover all anticipated short and medium-term requirements.
The solution adopted
The result of this collaboration has been a warehouse distributed into the following zones:
- Automated pallet warehouse for oversized a/o bulky consumer products.
- Automated miniload warehouse for spare parts, accessories, and small and medium-sized products.
- Picking stations for orders coming from the automated pallet warehouse.
- Picking stations for orders coming from the miniload warehouse.
- Consolidation and packaging area.
- Preloads of completed orders.
- Receipt of orders.
- Loading docks.
- Area for future expansion.
- Offices and utilities.
Automated pallet warehouse
It consists of three aisles with double-deep racks placed on both sides, allowing a storage capacity of 2,358 pallets of 1,200 x 1,500 mm. Double-deep racks increase the capacity of the available space and reduce the total cost of the installation. A stacker crane, placed in each of the aisles, is responsible for moving the pallets between P&D stations and the locations, and vice versa.
The picking stations take prominence in the design of the front of the warehouse, as represented by the illustration on this page. The general set up takes into account products that are rarely issued in full pallets. The reason being that most of the orders received by BH Bikes are composed of few and varied SKUs.
Each of the picking stations, attached to the main conveyor circuit of the warehouse, has two positions for pallets of origin and four for destination pallets. Operators are assisted by a raised platform that facilitates the handling of large packages and can work in waves of four orders at a time.
At picking stations, the needed computer equipment is set up to perform all functions, guided and managed by the Mecalux Easy WMS.
Miniload warehouse for boxes
The miniload warehouse has been allocated for all medium and small-sized SKUs, especially accessories and spare parts that have already been placed into plastic boxes, more precisely, 800 x 600 x 320 mm euro boxes.
In each of the aisles, a single-mast stacker crane with a single blade extractor was installed, which can transport boxes of up to 100 kg. Boxes, depending on the size and volume of the product, can be subdivided to accommodate up to four different SKUs.
The miniload installation has a conveyor with double recirculation that supplies boxes to the two picking stations. This picking area, shaped like a "U" allows three boxes in accumulation ― not counting those circulating on the conveyor itself ― whose objective is to work with greater fluidity.
Prepared items are initially introduced into medium-sized carts. When the order is completed with items from the miniload warehouse, it is moved to the packaging and labelling tables to be consolidated with the rest of the prepared products in the pallet racking warehouse. Once the process is finished, the order is taken to the area reserved for preloads and prepared orders.
Given the size and weight of the boxes, and the number of requests that are made, it was decided to carry out product replenishment at the picking stations, taking advantage of off-peak hours, when less picking is performed.
Easy WMS: the brain of the installation
Easy WMS, the Mecalux warehouse management system, is responsible for the warehouse working in a coordinated manner in all areas and does it via various previously parameterised rules.
The WMS is tasked with managing the following: entry of goods, allocation of the most appropriate location according to logical optimisation criteria of spaces and consumption, the output of load units, management of picking, issuing of documentation, consolidation and dispatch of orders, etc.
Also, and through its Galileo Control module, it manages the movements of all the mechanical elements, mainly of the stacker cranes and conveyors. Thus, it enables load units to circulate in the most logical and optimal route, as well as cutting down order fulfilment times.
Easy WMS is permanently connected to the ERP or primary management system of the company, exchanging data and commands for the efficient integrated business management of BH Bikes.
Advantages for BH Bikes
- Maximum use of space: the miniload facility is enabled to store 3,672 boxes, whereas the automated pallet warehouse allows for a 2,358 pallet capacity.
- Lower costs: the company has lowered logistics and personnel costs by centralising operations and by automating storage systems.
- Better service: warehouse automation allows for increased production volume and reduces errors by 99%, offering faster and higher-quality service.
- Total warehouse control: thanks to the Mecalux Easy WMS, BH Bikes manages all vital functions within general operations.
Automated pallet warehouse | |
---|---|
Storage capacity: | 2,358 pallets |
Pallet size: | 1,200 x 1,500 mm |
Warehouse height: | 14.3 m |
No. of stacker cranes: | 3 |
Extraction system: | double-deep |
Load levels: | 6 |
Gallery
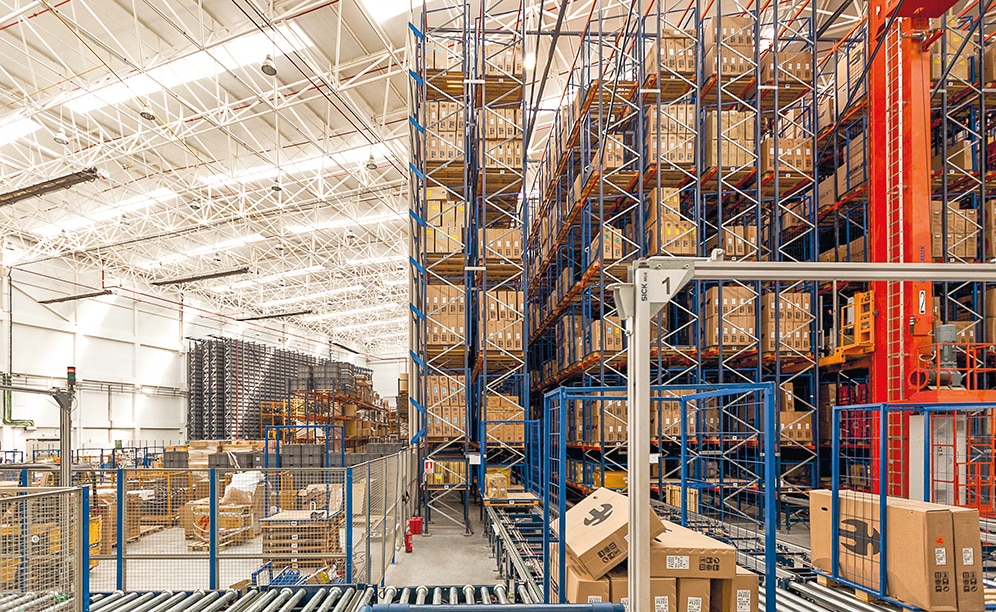
This new centre, consisting of a miniload and an automated warehouse for pallets, has centralised all logistics activities of BH Bikes group
Ask an expert