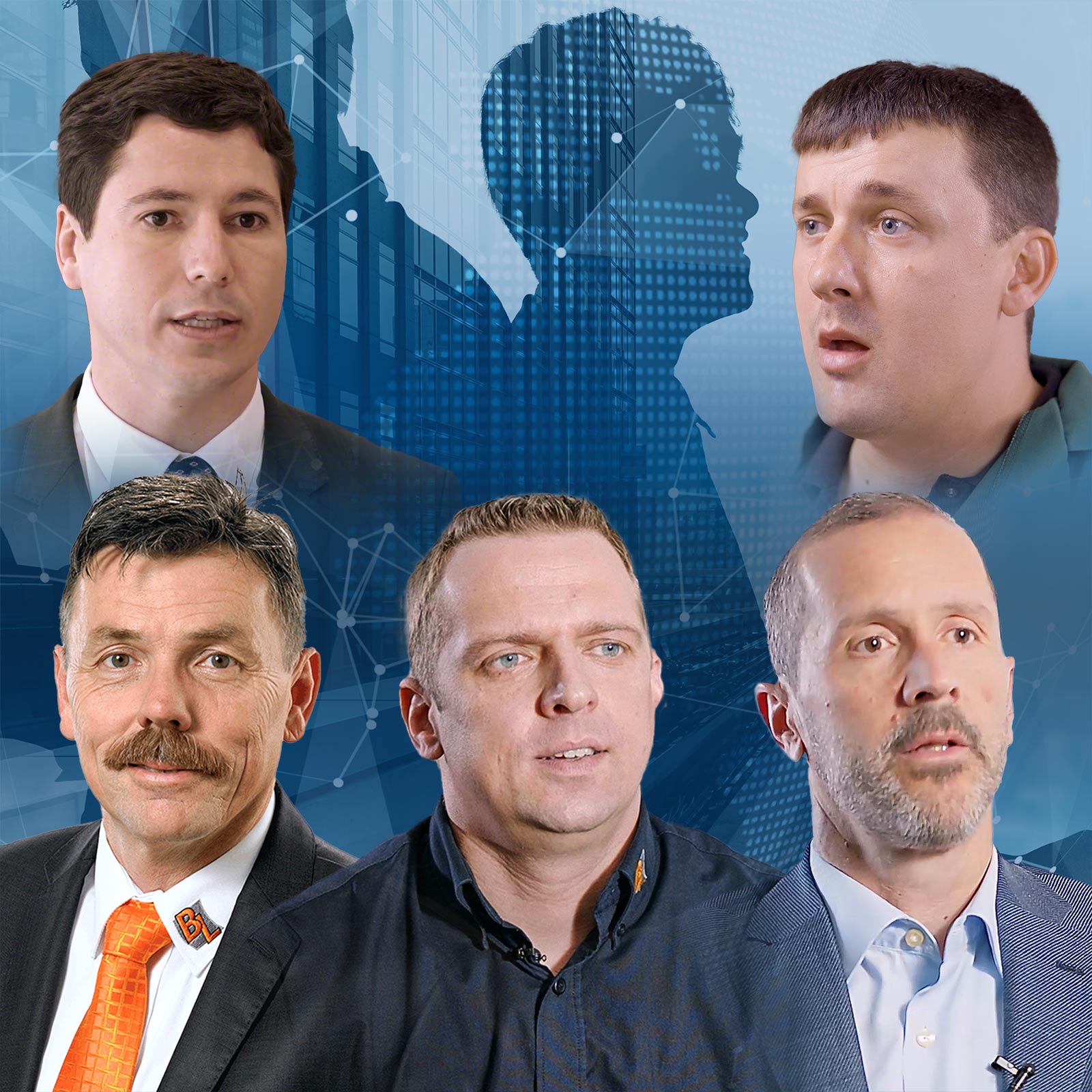
Customer satisfaction, our top priority
Successful implementations in small, medium-sized and large companies across all sectors
Partnering with a technology company like Mecalux gives our customers a competitive advantage with comprehensive solutions and storage designs tailored to their needs.