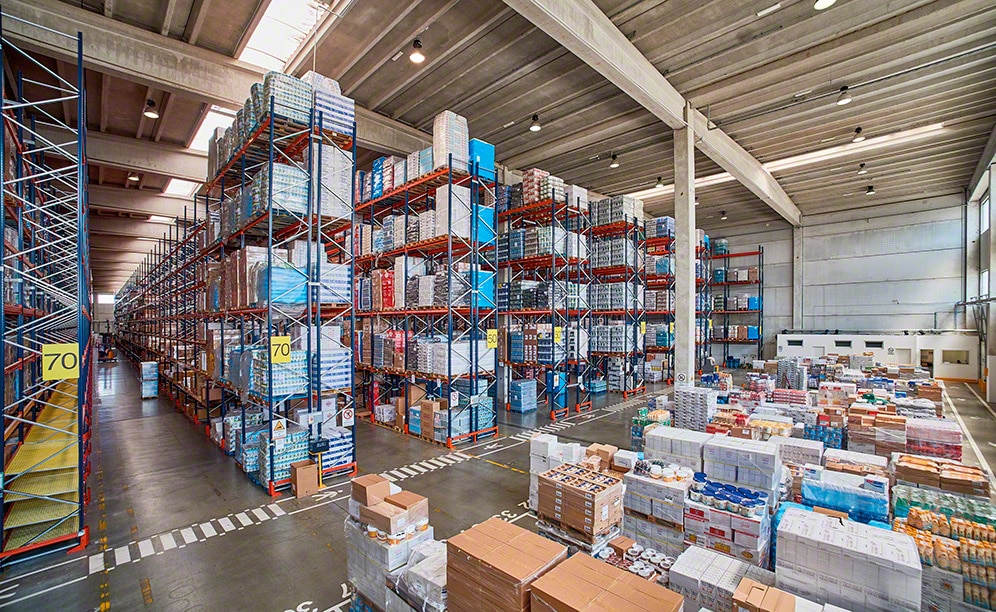
The logistics operator Ekom equals effective picking
Pallet racking for Ekom warehouse provide a capacity to store more than 14,400 pallets
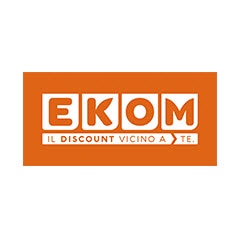
Mecalux has supplied pallet racking in the new warehouse Ekom owns in the town of Tortona (Italy). This solution offers a storage capacity of more than 14,400 pallets and direct access to products, which speeds up storage and picking work.
The Ekom warehouse
This logistics operator needed to max out the storage capacity in its distribution centre in order to deposit its customers’ products, mainly manufacturers of industrial supplies and consumer goods.
Likewise, it needed to boost picking and order consolidation speeds.
Bearing these requisites in mind, Mecalux set the warehouse up with 10.5 m high, 116 m long pallet racks. SKUs are slotted in the corresponding locations based on their turnover.
The proper distribution of the goods has achieved optimised operator workflows, while increasing the number of cycles.
Pallet racking
The pallet racking system is suitable when housing a lot of pallets with many different SKUs of various weights, sizes and dimensions. Plus, this system adapts to any kind of unit load.
Direct access to products streamlines the management of goods and order preparation. This warehouse is operated by fork trucks when pallets are inserted and extracted from their locations and by ground level order pickers allocated to picking tasks.
Due to the length of the racks, an underpass was opened up in the central part of the warehouse that facilitates operator workflows. The level immediately above the passageway is protected by electro-welded mesh, which guarantees load stability and prevents materials from falling.
Picking
Product is picked off the lower levels of the racks. Either the boxes are taken directly from the pallets or small-sized items from the live picking shelves.
These shelves are filled with slightly inclined roller tracks, so boxes slide via gravity to the front of the lane. Items are taken from inside the first box, and reserve product boxes accumulate behind.
This system streamlines picking by cutting down on the movements of the operators. So, workers do not need to crisscross the entire warehouse to collect the items for each order. Instead, they only work in one specific zone.
In the case of high demand products, one of its main advantages is that both replenishment and pickup of these products can be done at the same time, without interference between the two operations. Replenishment takes place in the loading aisle, located opposite to the one for order picking. Operators insert boxes into the levels, and these move to the opposite end on their own.
On the other hand, the replenishment of lower demand products is carried out in the same aisle where orders are prepared. This makes full use of off-peak periods, i.e., when there is a smaller volume of orders to put together. Boxes are inserted and pushed into the corresponding locations, one after another into each channel.
Receptions and dispatches
In front of the racks is a wide receiving and dispatching area, including space for ground level preloading. Pallets are grouped according to the order or route, ready for their final distribution.
Advantages for Ekom
- Adaptable picking: by organising goods according to their size and turnover, this optimises operator workflows during picking.
- Well used space: the entire warehouse surface has been fully utilised to obtain the large storage capacity that was needed for such a sizeable number of SKUs.
- Accessible goods: direct access to the products is essential to speeding up order picking.
The new warehouse Ekom | |
---|---|
Storage capacity: | 14,472 pallets |
Pallet size: | 800 x 1,200 mm |
Racking height: | 10.5 m |
Racking length: | 116 m |
Gallery
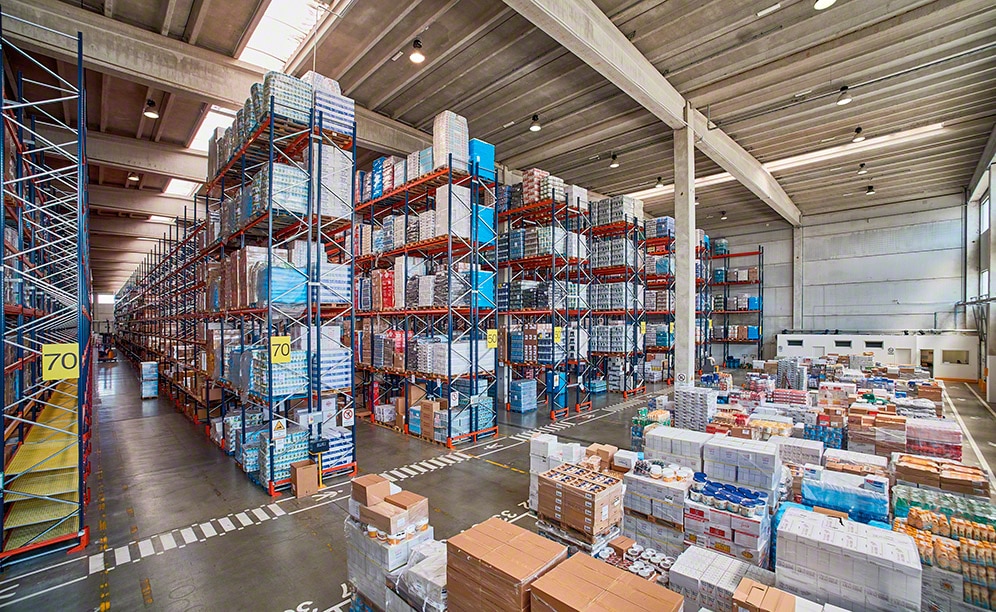
Mecalux ha suministrado estanterías de paletización convencional en el nuevo almacén que Ekom
Ask an expert