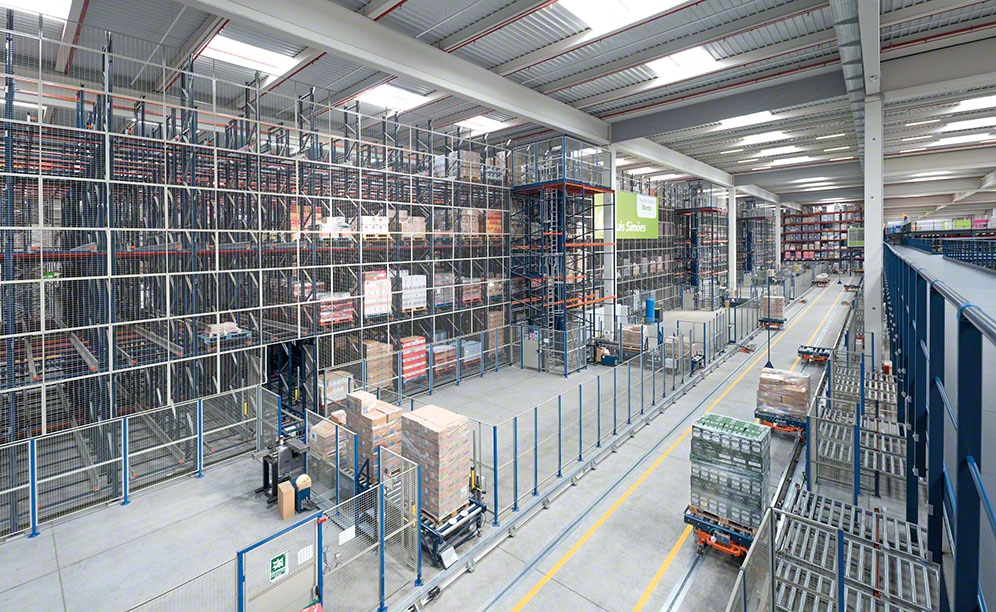
The Luís Simões logistics centre in Cabanillas del Campo (Guadalajara)
Luís Simões' warehouse in Spain has pallet racks and an automated warehouse sequencer
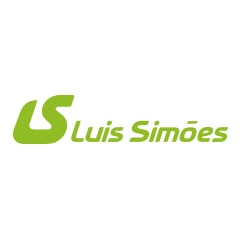
The renowned logistics operator Luís Simões has a modern centre in Cabanillas del Campo (Guadalajara, Spain) where it stores nearly 100,000 pallets and prepares more than 4,000 daily orders. At the core of this centre is a warehouse equipped with the automatic Pallet Shuttle system with Mecalux transfer cars. It acts as a buffer and fulfils the role of organising, sequencing and programming the prepared orders to be distributed. All this is managed by the powerful, efficient Easy WMS software from Mecalux.
Transport and logistics solutions
Founded in 1948 in Loures (Portugal), Luís Simões is a logistics operator offering transport, storage and picking solutions to all types of companies.
Present in the Spanish market for over 30 years, the firm manages a massive fleet of 2,100+ vehicles and works with over 2,500 collaborators. Luís Simões provides comprehensive logistics services in 25 warehouses occupying around 400,000 m2 in 10 different regions on the Iberian Peninsula.
Logistics centre features
The company has set up a modern 66,000 m² logistics centre in Cabanillas del Campo (Spain). This town is very close to Madrid and has become a strategic hub for large logistics operators such as Luís Simões.
The new centre contains two warehouses in which operators manage stock and prepare orders for all its customers from numerous sectors (mainly food, beverages, perfumery, cosmetics and retail), as well as two tax warehouses for beverage clientele. To cope with the e-commerce boom, the company also provides B2C adapted solutions and runs a Co-Packing service.
After Mecalux fitted out a Luís Simões warehouse in Porto (Portugal)—with more than 35,000 pallets in pallet racks and compact racking with the Pallet Shuttle system—, the renowned logistics operator contacted Mecalux yet again to commission its new warehouse in Guadalajara.
On this occasion, a storage solution was needed to facilitate the management of a wide variety of products from companies with just as diverse needs. For this very reason, Mecalux installed 12.5 m high pallet racks with an overall 93,241-pallet capacity for different pallet sizes, specifications and demand levels. However, the company’s priority was to streamline and optimise preparation and dispatch of 4,000 orders per day. Because this is such a high number, it required a system to help it organise finished orders. Mecalux came up with the solution: an automated warehouse equipped with the Pallet Shuttle system and transfer cars managed by Easy WMS. The warehouse is tasked with sequencing and scheduling order dispatches of ready orders based on vehicle routes, combining efficiency and cost-efficiency.
Automated warehouse: order sequencing
At the heart of this logistics facility is the fact that order-picking work done off pallet racks is combined and consolidated at this location. Thanks to this warehouse, the company has a space where it can group and organise its orders.
The automated warehouse consists of two 12.6 m high blocks of racking, with four storage levels that can hold six pallets deep. It has storage capacity for 2,556, 1,200 kg pallets.
At each level, two transfer cars serve the storage channels. To do so, a Pallet Shuttle moves inside the channels to insert or extract the goods. With two transfer cars per level, the installation’s performance is higher and it can operate non-stop. For example, while preventive maintenance is being carried out on one transfer car, the other shuttle is still in operation.
Sequencing is a cornerstone of this logistics centre, given that grouping orders by transport route and sending them in the specific order to deliver to customers is a must. The Mecalux Easy WMS warehouse management system takes centre stage at this point. Its mission is to identify, locate and order the dispatch of each pallet that arrives at the automated warehouse according to the pre-established sequence.
The warehouse sequencer has five entry points. Three of them have a pallet lift that moves the pallets to one of the upper racking floors. Meanwhile, the other two are used to store the pallets on the lower level (in particular, higher rotation products to speed up dispatch).
At warehouse sequencer infeeds, Easy WMS identifies each item and assigns it the most suitable location depending on when it will be shipped out. After all, a sound goods distribution in a warehouse optimises automatic handling equipment movements and, consequently, orders.
António Martin - Luís Simões Logistics Centre Supervisor in Cabanillas del Campo
“Thanks to the automated warehouse, we have increased the flow of goods in and out of our business, optimised the vehicle loading process and reduced errors.”
Benefits of installing an automated warehouse sequencer
Delivering orders on time to customers and in the set order is high on any company’s agenda. For this to be feasible, there must be strict organisation of warehouse operations and appropriate storage systems.
Installing a sequencing warehouse like Luís Simões has done is an excellent solution. Orders can be sequenced based on different criteria such as the route of the transport vehicles or the nearest or furthest delivery point, as well as the most convenient route.
In addition, an automated warehouse provides:
- Traceability of goods.
- Maximum use of space.
- Optimisation of storage capacity and product movements.
- Possibility of modifying deliveries according to newly established criteria.
- Real-time inventory.
- High productivity.
- Goods safety and lower risk of accidents.
- Non-stop operations.
Sequenced dispatch of goods
The sequencer warehouse has five exit points that connect directly to an inverted monorail system (IMS) on the floor. Like the infeed points, three outfeeds have a lift that connects the four floors, while the lower two are used for product storage.
Directly opposite, the IMS moves the pallets straight to the preload channels in the sequence established by Easy WMS beforehand. Dynamic potential and easy assembly have been decisive factors in this pallet transport system’s implementation, the main benefit of which lies in the smooth, safe movement of orders.
For Luís Simões, solid organisation of the dispatch area has been of fundamental importance to make sure orders are distributed in the correct sequence. Ten sets of three live preload channels (14.2 m long) have been installed.
The merchandise from each will be loaded onto that channel’s specific delivery lorry. A monitor has been installed at the top of the channels. Here, Easy WMS shows operators highly detailed information on the dispatch-ready pallets: which pallet to remove first, the total number of available pallets in the channel, etc. With all this data, the possibility of errors is greatly reduced. Operators scan each pallet using a radio frequency pistol. This ensures that the goods are loaded into the lorry in the proper order.
In the dispatch area, a conveyor circuit is used for cross-docking. So, goods with no need to be stored on the racks bypass the automated warehouse to follow the order sequence established by Easy WMS.
The heart of the logistics centre
A sophisticated logistics centre such as Luís Simões’ in this site not only stands out for its high storage capacity (around 100,000 pallets), but also for its efficient organisation of orders. There are no errors or delays in supplying customers due to this warehouse.
The sequencing buffer is what drives this logistics centre, sorting and organising the 4,000 orders prepared daily in a coordinated, orderly manner and then distributing them in the right order at the right time. All this, of course, would not be possible without Easy WMS’s guidance. Mecalux’s warehouse management system directs and sequences orders keeping the company’s requirements in mind.
Rui Simões - Logistics and Innovation Manager at Luís Simões
“Thanks to Mecalux’s storage solutions, we have achieved major increases in operational efficiency and effectiveness. Besides, to store as many pallets as we hold, we would need 9,000 m² of space. But, with the automated warehouse, we occupy only 6,500 m². Impressive!”.
Advantages for Luís Simões
- Nearly 100,000 pallets: pallet racking’s versatility makes it possible to store pallets with variable weights and volumes. The stored goods can be up to 3 m high.
- Shipment sequencing: the automated warehouse is responsible for sequencing prepared order shipments according to the transport vehicle routes.
- High performance: by having a fully automatic solution, the warehouse sequencer works tirelessly organising orders based on the delivery route.
Logistics centre of Luís Simões: Pallet racks | |
---|---|
Storage capacity: | 93,241 pallets |
Pallet size: | 800 x 1,200 mm |
Max. pallet weight: | 1,200 kg |
Racking height: | 12.5 m |
Gallery
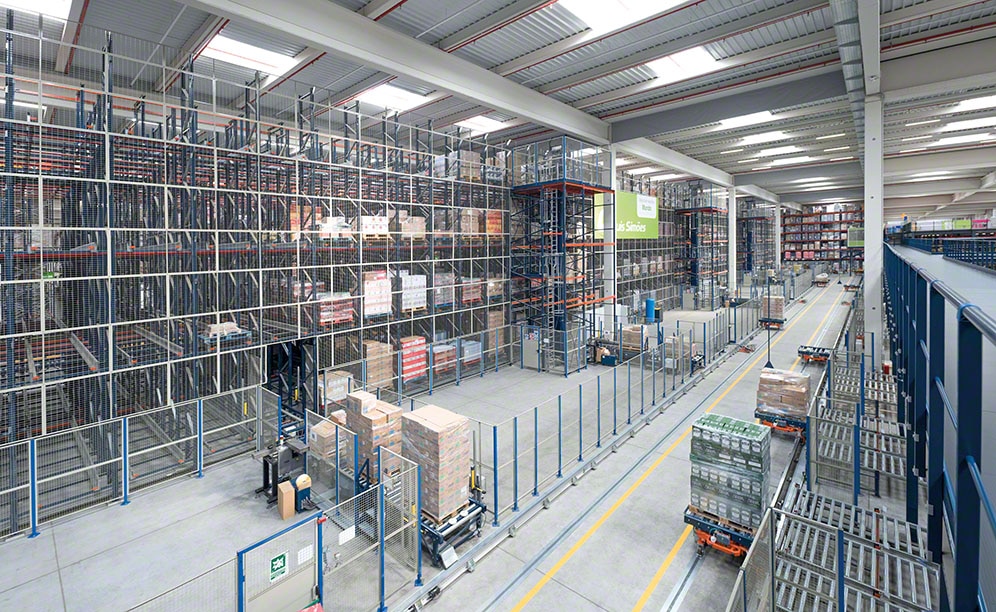
Luis Simoes automated warehouse sequencer in Spain
Ask an expert