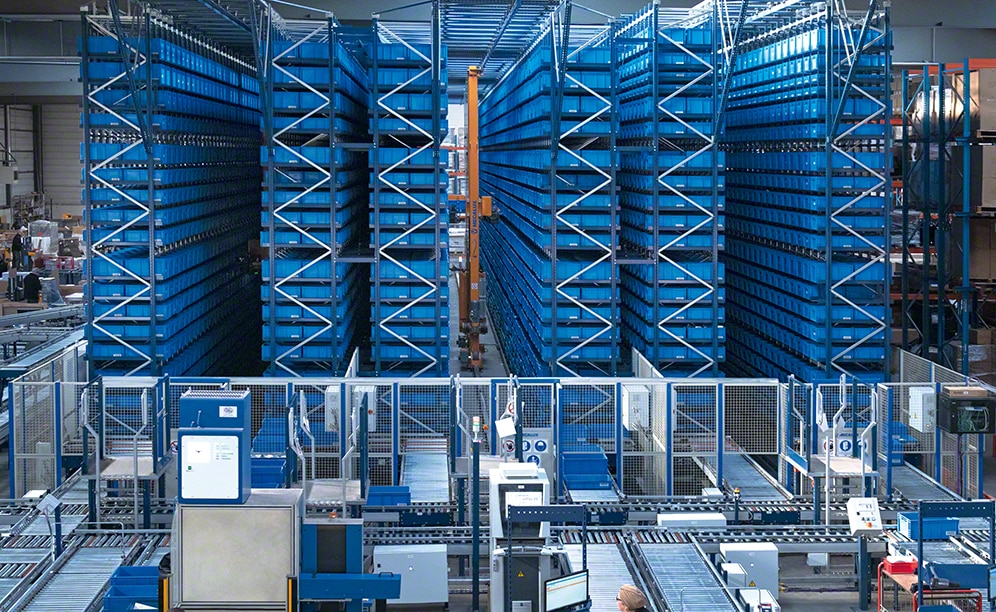
SAM Outillage: a productive tool
SAM Outillage stores 10,000 SKUs and delivers orders in just 24 hours
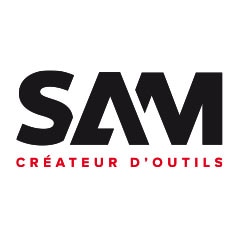
Tool manufacturer SAM Outillage has gone from having an overloaded, outdated warehouse to leveraging each and every millimetre and even increasing its throughput. All of this was achieved through the installation of an automated warehouse for boxes managed by Easy WMS and pallet racking for bulky products. In its 6,000 m² logistics centre in Saint-Étienne (France), SAM Outillage stores 10,000 SKUs and delivers its orders in just 24 hours. A large area for goods receipt along with order picking and kitting stations have been set up around the automated warehouse, speeding up the work of operators. After modernising its warehouse, the company has increased the productivity of all its operations by 25%.
The company
Founded in 1921, SAM Outillage is a family business specialising in the design, manufacture and marketing of hand tools used in maintenance, servicing and repair operations for the industry and automotive sectors. The 10,000 items supplied by SAM are divided into five families:
- Traditional tools: fastening, bolting, gripping, measuring and cutting instruments.
- Storage to optimise work stations: workshop equipment, cabinets and toolboxes.
- Tyre tools.
- Measuring instruments.
- Automotive tools: mechanic and body shop equipment, etc.
Innovation has always been the mainstay of SAM’s growth. According to Didier Denizot, the company’s Logistics Director, “over the next few years, we have before us the challenge of becoming the market-leading manufacturer of smart tools. To that end, it is vital that we have an Industry 4.0 factory with automated logistics.”
Transformation into a high-density storage area
SAM Outillage has a five-hectare industrial complex in Saint-Etienne that includes the head office, R&D area, manufacturing plant and logistics centre. “It was clear to us that we had to improve our goods management — from receipt through to dispatch — increase storage capacity by 50% and ensure the utmost safety of our operators,” says Didier Denizot.
To undertake this modernisation, SAM sought the cooperation of Mecalux, a cutting-edge multinational in the storage system market that, in the words of its logistics director, “has adapted to our needs and resolved any questions we had.”
Renovating the warehouse is no easy task, as it requires an exhaustive study of the space, the operations and the needs that must be met. The result, however, has been very positive. As Denizot explains, “it has been a success from both a technical and human point of view. We visited other installations fitted out by Mecalux to see how they worked and to assess their strengths and weaknesses. This project called for the creation of a team dedicated to developing the most suitable solution that was made up of SAM employees (especially the team from the logistics centre, in order to prepare it for the change) and specialists from Mecalux.”
Mecalux proposed the installation of pallet racking, an automated warehouse for boxes, and conveyors conveyors to serve the different work areas: receipt, product personalisation, kitting, and order preparation and dispatch. Easy WMS, Mecalux’s warehouse management system that efficiently runs the automated warehouse processes, was also implemented.
The pallet racks stand 8 m high and provide storage capacity for 6,030 pallets. Designed to accommodate loads of different sizes, weights and shapes, this racking is used for bulky products such as tool trolleys. The automated warehouse for boxes, meanwhile, can store 80% of SAM Outillage’s SKUs.
This system was chosen primarily to stock items more densely, as it is able to hold a large number of products in a limited space. The installation is made up of three aisles with 40-metre-long double-deep racking on each side that can accommodate up to 20,000 boxes measuring 400 x 600 mm with three different heights.
With this solution, the company has not only maximised its storage volume, but also grouped into one area all the operations required to manage small-sized goods (receipt, kitting, picking, packaging and dispatch).
Didier Denizot notes, “By modernising the warehouse, we have restructured our entire logistics infrastructure. We have streamlined the flow of goods, and order deliveries are much quicker. We can now ensure that our products will be delivered in 24 hours, especially orders received before 4:00 p.m. that require next-day delivery.” SAM Logistics Manager Candice Aubert adds, “The automated warehouse by Mecalux has helped raise our productivity by 25%.”
Advantages of the automated warehouse for boxes
- High productivity and availability. Automation minimises errors and reduces the number of movements within the warehouse.
- Accessibility to stored products. Conveyors and stacker cranes move and store goods quickly and safely.
- Optimum use of space. The racks leverage the entire surface area to provide the best possible storage capacity.
- Speedy order preparation and dispatch. The “product-to-person” principle considerably reduces time spent on picking and kitting.
- Cost savings. Faster order preparation, increased productivity and optimal use of space all lead to a quick return on investment.
Didier Denizot - SAM Logistics Director
“The automated warehouse has provided us with many advantages, among which are greater speed and responsiveness, smooth product flows (from goods receipt through to the dispatch of orders to our customers), increased storage capacity, improved working conditions for operators, and raised productivity.”
Picking and kitting operations all in one place
Multiple operations take place in the automated warehouse for boxes: product receipt and oversight, kit creation, tool personalisation via laser engraving, and order preparation and dispatch.
The kits comprise sets of tools stored in cases for easy handling and transport. Order prep consists of grouping together all the items ordered by customers (individual tools or kits).
The automated warehouse is specifically designed to speed up kitting and picking operations because of these two reasons:
- “Product-to-person” principle. “Before renovating our centre, operators would walk around the warehouse for 10 to 12 km a day to locate the SKUs they needed. With the automated warehouse for boxes, goods are moved to the picking stations automatically. This project is completely in line with our corporate social responsibility framework,” points out Candice Aubert. Once the boxes are received, the operators merely need to remove the items from inside and place them in the corresponding order.
- Easy WMS management and monitoring. According to Aubert, “this system orchestrates the movements of the stacker cranes and, in addition, provides continuous inventory control.” Knowing the status of the goods is vital for preventing stock-outs and always delivering the expected quality of service.
At the front of the warehouse are two stations where kits are put together. Each of the workstations is wide enough for operators to sort the tools and place them quickly into the cases. On one side of the warehouse, three picking stations have been installed.
Candice Aubert explains, “We have gained numerous advantages with the automated warehouse for boxes: reliable and continuous stock control, as well as improved adaptation to peak workloads. We have cut dispatch times and ensured delivery in less than 24 h, not to mention streamlining and boosting productivity throughout the entire order preparation process. Furthermore, we have room to install a fourth picking station, which will increase our order volumes.”
Each operator can prepare up to nine orders simultaneously: four in boxes, four in envelopes and one on a pallet. The operators remove the units from inside the boxes automatically brought to them from the warehouse and place them in the corresponding orders. Once the orders are finished, they are moved to the area in which they will be consolidated with bulky products from the pallet racks. These completed orders are then packaged, banded and labelled, and the document required for their dispatch is issued.
Candice Aubert - SAM Logistics Manager
“The automated warehouse for boxes has given us a whole host of advantages, most importantly, reliable and perpetual stock control and improved adaptation to peak workloads. In addition, we have reduced order dispatch times and can ensure that purchases arrive on schedule. It should also be noted that we have sped up and boosted productivity throughout the entire picking process.”
A high-throughput warehouse
Multiple garages and companies need specific tools to provide the service their customers expect. To make this possible, SAM Outillage requires its logistics to be flexible and efficient and its wide range of products to be available at all times.
SAM has condensed the storage of its 10,000 SKUs by simplifying all processes, from product receipt through to order dispatch. The result of this transformation, which has generated a 20% rise in productivity, is reflected in an improvement in the quality of service provided to its customers.
Advantages for SAM
- Optimised surface area: the implemented storage solutions leverage all available space. The automated warehouse for boxes, for example, manages 80% of the stock (up to 19,448 boxes) in just 30% of the logistics centre’s total surface area.
- Productivity in kitting and picking tasks: the automated warehouse supplies the work areas specially enabled for the operators to prepare both the kits and the orders more quickly. Automation has raised operational productivity by 25%.
- Speedy receipt: the two receipt stations expedite the entry of goods, while the conveyors move the items to the automated warehouse.
- Increased responsiveness: SAM can deliver up to 10,000 SKUs to its customers in just 24 h.
- Organisation of stored goods: combining pallet racks with the automated warehouse for boxes in the same space helps to sort the 10,000 SKUs by characteristics and turnover.
- Improved working conditions for operators: automation prevents operators from having to move around the warehouse to pick products, as well as stacking empty boxes.
Pallet racks | |
---|---|
Storage capacity: | 6,030 pallets |
Racking height: | 8 m |
Gallery
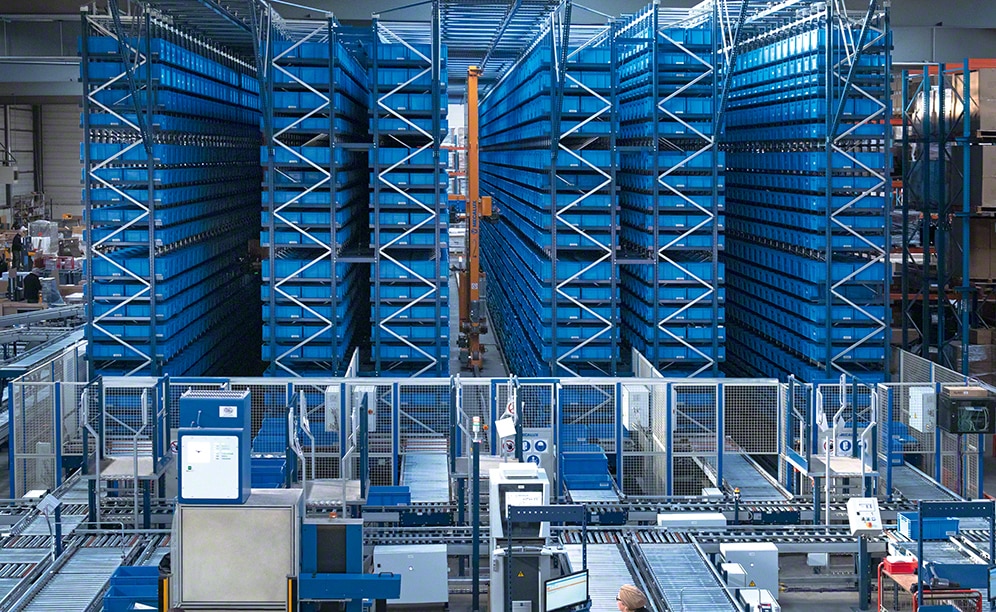
SAM Outillage's warehouse for boxes in France for hand tools
Ask an expert