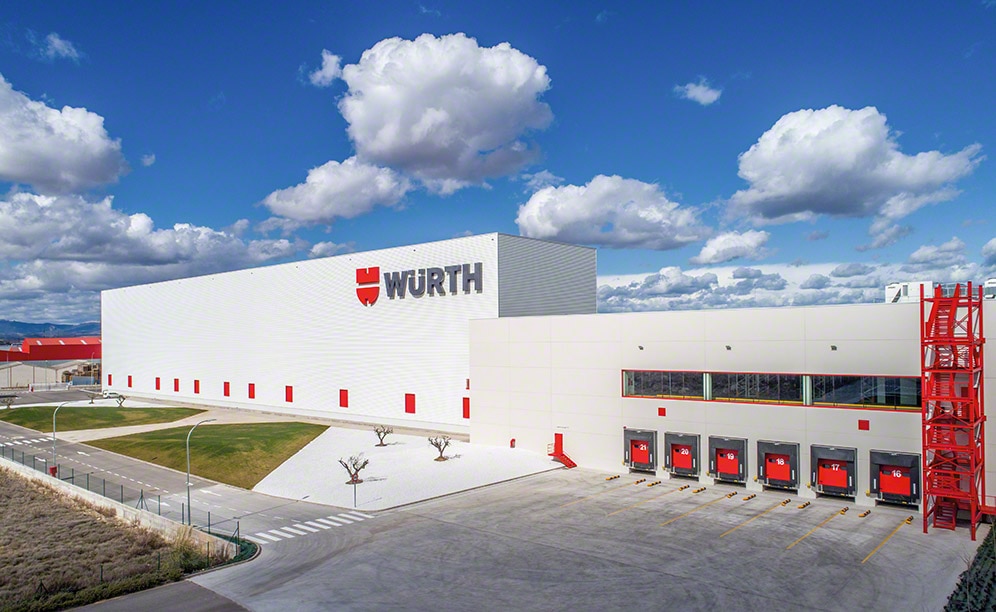
A 100% automated, turnkey warehouse for Würth in La Rioja
Würth warehouse holds full catalogue of tools, bolts, shims and drill bits in a new centre in La Rioja.
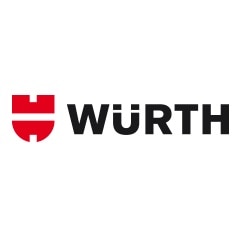
Würth, a multinational company, celebrated its 40th anniversary of doing business in Spain by expanding its facilities in Agoncillo (La Rioja) with solutions designed, manufactured and installed by Mecalux. Recently, the company opened a new reception and dispatch building, as well as a fully automated clad-rack warehouse for pallets. The automated warehouse, with capacity for 15,190 pallets, can move up to 300 pallets/hour, helping to keep the high service level that Würth guarantees its customers for order deliveries across Spain.
Würth: over 40 years in Spain
Würth is a German company that sells all types of fasteners, connectors and assembly components for the construction, automotive, chemical, and plumbing sectors, among others. Its extensive product catalogue, comprising over 125,000 SKUs, includes screws, plugs, drilling and cutting instruments, tools, workwear, etc. The company was founded in 1945 in the small town of Künzelsau (central Germany) as a wholesale screw business. Its headquarters are still there and the firm now employs around 74,000 people in over 80 countries on five continents.
Spain’s 250,000 potential customers are what drew Würth to this country in 1977. It set up its headquarters and a logistics centre in Palau-solità i Plegamans (Barcelona) and another logistics centre in Agoncillo (La Rioja). The Spanish division has become one of the largest companies within the Würth Group (after the German headquarters). In recent years, it has expanded and modernised its logistics centre in La Rioja to spur on this growth. Next to the original warehouse, an automated clad-rack warehouse, a loading-dock building and additional parking spaces for employees and visitors were built. One of Würth’s requirements was that operations being carried out at its logistics centre should not be affected during the implementation. According to Pedro Montenegro, Würth Spain’s logistics director, “We have worked very closely with Mecalux’s engineers and project managers to ensure that the works did not affect our customers at any time.”
This warehouse easily meets the company’s requirements, without forgetting its growth prospects and, as such, space has been reserved for future expansion. Technology has been one of the driving forces behind Würth’s growth. For this reason, the logistics centre also has the most modern equipment to store and transfer goods to the other areas automatically, with minimal involvement by the operators.
Mecalux has designed the conveyors, stacker cranes, pallet lifts and electrified monorail systems (EMS) to guarantee the flows desired by the company to supply customers in the shortest timeframe. In addition, Würth’s corporate colours were even applied to components, showing Mecalux’s great attention to detail. In other words, the racks, stacker cranes, electrified monorail system, pallets lifts and conveyors are all red and white.
Pedro Montenegro - Logistics Manager at Würth Spain
“It was essential for us to find a partner. To find a company we could identify with and feel that, in the long term, we could continue carrying out large-scale projects together. Mecalux was and is a perfect fit as a partner in all our logistics expansions.”
Clad-rack warehouse: the racks support the building
The considerable dimensions of the automated clad-rack warehouse make it stand out in comparison to other buildings: it is 26 m high, 115 m long and 23 m wide.
Working with tens of thousands of SKUs was a challenge for the company. So, it was essential to take advantage of available space to provide the maximum potential storage capacity. According to Pedro Montenegro, "one of the great advantages of the solution installed by Mecalux is that in just 3,500 m2 we can store up to 15,000 pallets. With a pallet rack warehouse like the ones we had before, frankly, that was just impossible.”
The warehouse consists of five aisles with single-deep racks on each side, each with a corresponding stacker cranes for inserting and extracting goods. These machines work at a travel speed of 220 m/min and a lift speed of 54 m/min. They can move up to 300 pallets per hour in combined cycles, that is, entries and exits are performed simultaneously.
The entire warehouse is controlled by Mecalux’s Easy WMS warehouse management system, which works in conjunction with the Würth computer system to track all goods during their entry, exit and storage.
The installation includes two pallet lifts. One connects the reception and dispatch area (lower floor) with the automated warehouse’s entry and exit points (upper floor). The other pallet lift lowers the pallets from the automated warehouse to the bottom floor of the existing warehouse.
A building attached to the warehouse
A 15 m high building has been erected between the new automated warehouse and the previously built warehouse. It is divided into two floors, each set aside for a different operation.
Lower floor
Product inputs and outputs are done on the lower level through twelve loading and unloading docks. To this end, a conveyor circuit has been installed with three entry and two exit points. These pallets must cross a pallet checkpoint where the load weight and dimensions (gauge), and the condition of the pallets (spaces, blocks and skids) are checked and the product is identified by reading the barcode label. Incoming single-SKU pallets are verified on this floor. Pallets with more than one SKU are temporarily placed on the racks, and later checked on the upper floor.
One of the incoming lines has an automatic system that supplies slave pallets to pallets that are in poor condition. Once the goods have passed the checkpoint, a pallet lift raises them to the top floor for entry into the automated warehouse.
This pallet lift also lowers the pallets from the automated warehouse to the dispatch area. At the exit point, the slave pallets are retrieved, stacked and used again at the entry point. The pallets that are to be dispatched are grouped in the preloading area on the floor, just in front of the docks, based on if they correspond to the same order or transport route.
Upper floor
On the upper floor, an electrified monorail system (EMS) carries the pallets going into the automated warehouse up to the aisle assigned to them by Mecalux's Easy WMS. At the same time, the EMS trolleys collect the pallets going to the dispatch area and move them to the pallet lift, which lowers them to the bottom floor.
Multi-SKU pallets flowing from temporary storage are rechecked on this floor. Here, SKUs are separated and sorted, quantities are checked, products are identified and sent back to the automated warehouse.
Two picking stations have been set up in front of the electrified monorail system. There, full-box orders are prepared from the products stored in the automated warehouse. Speeding up this operation as much as possible was a priority for Würth; therefore, the installation was designed to supply up to 60 pallets/hour to each pick station. These stations are fitted out with the equipment needed to carry out the different tasks, including computers, label printers and pneumatic arms to facilitate product handling (which can be bulky and very heavy).
Using the pneumatic lifting units, the operators pick items directly off the pallets, which are brought to the picking stations by the electrified monorail system, and place these items on another pallet. The products that make up each order are grouped together on this other pallet. Up to eight orders can be prepared simultaneously at the two locations. On the upper floor, a conveyor circuit connects the new automated warehouse to Würth’s original warehouse. Said warehouse, with capacity for about 10,000 pallets, is designed for products that, due to their dimensions and product type (chemicals), cannot be stored in the automated warehouse. Moreover, small-sized units are also picked here. The conveyors supply the warehouse with the products needed for picking orders.
ADVANTAGES FOR WÜRTH
- Tailor-made solution: proactive surface usage yields a storage capacity of 15,190 pallets and space has been reserved for future expansion.
- High-tech warehouse: the new warehouse is fully automated, which ensures high, error-free workflows.
- Picking as a priority: the automated warehouse incorporates a specific full-case picking area and a conveyor circuit supplies the already-built warehouse with the goods needed to pick small-sized units.
Clad-rack warehouse: Würth Spain | |
---|---|
Storage capacity: | 15,190 pallets |
Pallet size: | 800 x 1,200 mm |
Max. pallet weight: | 1,000 kg |
Warehouse height: | 26 m |
Warehouse length: | 115 m |
Warehouse width: | 23 m |
Gallery
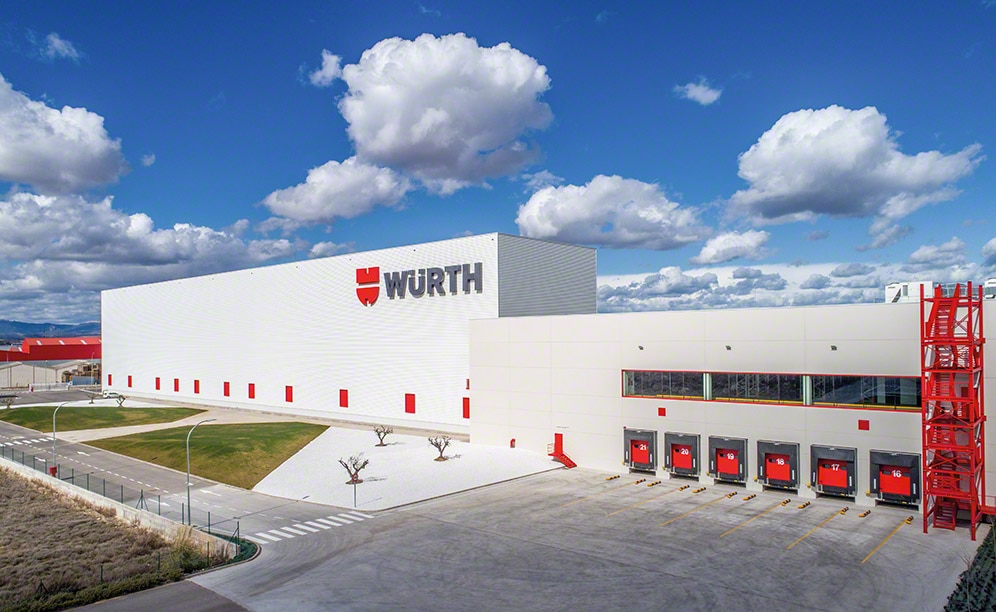
German company opens new warehouse in La Rioja (Spain)
Ask an expert